

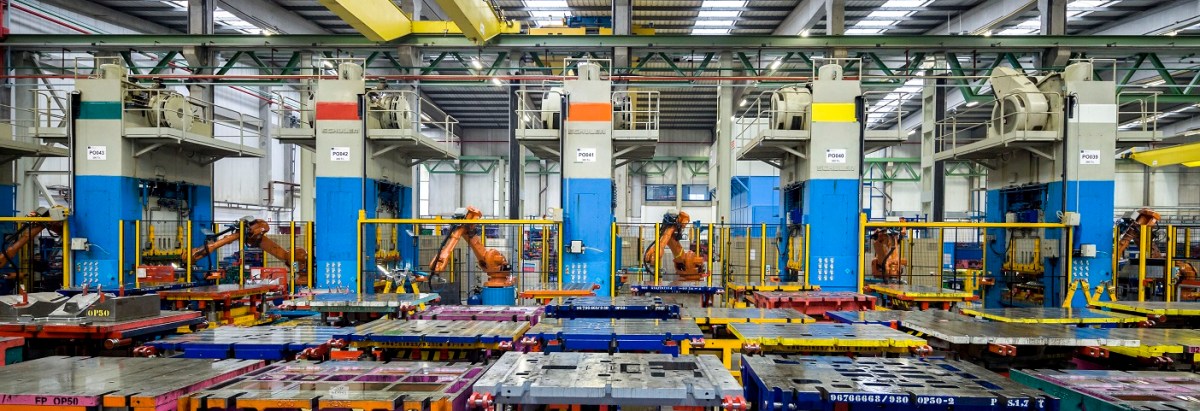
René González
Director de industria 4.0 y manufactura avanzada de Gestamp
La smart factory es una palanca para cambiar el modelo de operación de la industria, que ahora está basado en grandes series y economías de escala y que debe avanzar hacia un modelo mucho más flexible, manteniendo la eficiencia y la calidad.
Debemos contar con la mayor cantidad de información posible. Los datos son la esencia de la de la smart factory y la principal fuente de datos es el internet de las cosas (IoT). Disponer de un internet de las cosas lo más completo posible es lo que marca la diferencia, pero también es necesario que sea robusto, estándar y escalable.
Otro aspecto importante en el internet de las cosas que necesita la smart factory es garantizar que somos capaces de interactuar de forma bidireccional con las máquinas. Esto se consigue a través de una infraestructura que permita la interacción robusta del software con los autómatas programables y la robótica.

Por último, debemos disponer de sistemas de trazabilidad que nos permitan relacionar el mundo físico con el virtual. El objetivo final de cualquier industria es hacer productos mejores y de la forma más eficiente y flexible posible, por lo que necesariamente debemos poder relacionar los datos con cada producto y con el detalle de su fabricación de forma inequívoca, y para ello es necesario disponer de sistemas de trazabilidad física y digital.
Otras fuentes de datos son los sistemas tradiciones de gestión que existen en cualquier industria, como puede ser el Enterprise Resources Planning (EPR) o el Manufacturing Execution System (MES), además de fuentes externas de distintos tipos que en muchos casos se integran directamente en los sistemas tradiciones, como la demanda, por ejemplo, pero que en otras ocasiones es necesario recoger y tratar de forma específica. Incluso, en alguna ocasión, caso de datos relacionados con materia prima por ejemplo, se necesita aplicar los conceptos de trazabilidad antes mencionados para conseguir la necesaria relación de los datos con el mundo físico ya en la cadena de suministro.
En ocasiones puede ser necesario recoger el input de los empleados, más allá de lo que se informa a través de los sistemas tradiciones, y para ello solemos usar dispositivos wearables, smartphones o tablets con aplicaciones específicas.
Con todo ello, una vez resuelto el IoT, que sería el primer gran reto, el siguiente reto en la smart factory es la integración de los datos. Es imprescindible poder gestionar, controlar, acceder y explotar los datos, y para ello debemos crear entornos escalables que den soporte a volúmenes de datos extremadamente grandes, aceptando datos en distintos formatos que proceden de gran variedad de fuentes. Esto requiere dominar las últimas tecnologías de almacenamiento y procesado de datos y disponer de los entornos de procesamiento y las infraestructuras más adecuadas.
El gemelo digital es una réplica de un sistema físico. Se utiliza en industria y otros sectores desde hace muchos años como un entorno de experimentación para tratar de anticipar problemas sin afectar al sistema físico. Venimos de utilizar gemelos en nuestros proyectos de simulación que nos sirven para dimensionar las líneas de producción, los sistemas logísticos, o hacer virtual commissioning, entre otras cosas. Lo que hemos hecho en la smart factory es utilizar estos conceptos y el conocimiento adquirido para el caso de la gestión de plantas industriales completas o grupos de plantas, creando el modelo virtual o gemelo digital a partir de toda la información disponible.
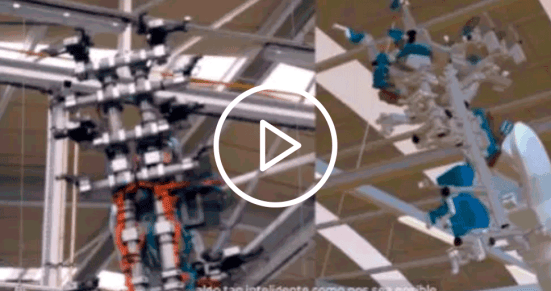
Si tenemos en cuenta la gran cantidad de datos que utilizamos, sobre todo procedentes del IoT como se ha explicado antes, tenemos una representación del mundo físico muy precisa sobre la que experimentar y trabajar.
A partir de aquí podemos utilizar modelos de simulación o modelos de machine learning (ML), dependiendo del tipo de predicción que queramos hacer. Los modelos de simulación se lanzan de forma masiva y automática cuando hay una desviación significativa en la fábrica para la búsqueda de los mejores escenarios, que se seleccionan mediante algoritmos genéticos que atienden a las prioridades de la fábrica, y los modelos de ML nos ayudan a predecir los problemas y las desviaciones antes de que ocurran.
Para el procesado de datos, los modelos de inteligencia artificial y las simulaciones, se precisa de mucha computación, memoria y almacenamiento, que a su vez tiene que ser distribuida y escalable.
A esto hay que añadir que en ocasiones necesitamos disponer de computación cercana, sobre todo cuando interactuamos de forma automática y bidireccional desde el mundo virtual con el mundo físico a través del IoT. Para ello contamos con soluciones Edge tradicionales, pero creemos que el MEC (Multi Access Edge Computing) de Telefónica va a ser determinante para simplificar, escalar y disponer de servicios para este tipo de aplicaciones que precisan de mucha fiabilidad y baja latencia.
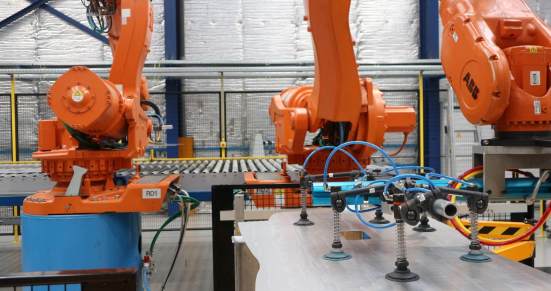
Si a esto añadimos que el acceso al Edge se realiza con una red 5G, podemos además llegar a un nivel de sencillez y flexibilidad tal que las máquinas pueden estar conectadas de forma completamente inalámbrica directamente con el MEC. Esta conexión inalámbrica habilita además la conexión de los vehículos que existe en cualquier fábrica para tareas logísticas, que al ser equipos móviles no admiten conexión por cable, además de otros equipos móviles como herramientas o embalajes, que no se conectarían si no es con soluciones inalámbricas.
El MEC nos permite por lo tanto disponer de un entorno de almacenamiento y procesamiento de datos con baja latencia y total flexibilidad.
La digitalización es un medio, no es un fin. La smart factory es en realidad la palanca que necesitamos para cambiar nuestro modelo de operación, que ahora está basado en grandes series y economías de escala y que debe avanzar hacia un modelo mucho más flexible, manteniendo la eficiencia y la calidad que nos caracterizan.
Disponer de fábricas flexibles capaces de adaptarse a las incertidumbres del mercado es lo que va a marcar la diferencia en un sector en el que se espera una profunda transformación, que no ha hecho más que empezar con la llegada del coche eléctrico.
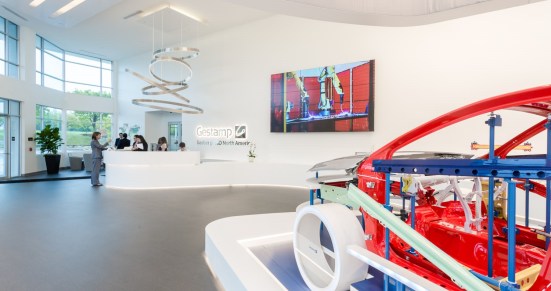
La razón por lo que la smart factory nos permite plantear modelos de operación más flexibles es porque permite gestionar entornos más complejos, y la flexibilidad supone necesariamente una mayor complejidad. No sería posible ir a un modelo de operación flexible sin un alto grado de control y de automatización a través de la digitalización.
Todas las tecnologías que nos permitan avanzar en la smart factory son necesarias y en este sentido la llegada del 5G nos ha abierto un mundo de posibilidades. La conectividad inalámbrica de alta velocidad, fiable y potente, con latencias ultra bajas, permitirá aplicaciones y casos de uso aun hoy inexplorados.
Seguimos con interés el desarrollo de la tecnología y cualquier nuevo caso de uso que se publica.
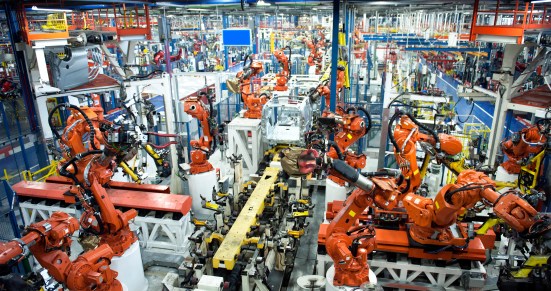
Recientemente hemos planteado un proyecto de I+D, junto con Telefónica y otros socios, que tiene como objetivo desarrollar nuevos conceptos de flexibilidad para la industria y donde el 5G es una de las tecnologías más determinantes.